The Search for Alternative Materials:
Flax Fibre Composite Bodies
A Quest for Sustainable Tone
For decades, the soul of an electric guitar has been tied to its wood. Mahogany, Ash, and Maple—sourced from old-growth forests—gave us the density, stability, and resonance that defined iconic sounds. But the world has changed. Those forests are vanishing, and the fast-grown plantation wood that has replaced them often lacks the quality we demand, resulting in instruments that are less stable and tonally inconsistent.
This project was born from a simple question: What if the future of guitar tone isn't wood at all, but something better? What if we could engineer a material that is not only 100% sustainable but also delivers superior acoustic performance?
The answer lies in a composite material crafted from renewable, natural resources: flax fibres for strength, bound together by a resin made from polymerized linseed oil and pine rosin.
By using locally sourced, renewable materials and hand-shaping the bodies, we avoid the immense environmental cost of traditional manufacturing. A hand-shaped composite body produces approximately 3.5 kg of CO₂. A commercially made wooden body, involving CNC machining and shipping exotic wood across the globe, can generate 8-12 kg of CO₂. That's a reduction of up to 70%.
V1 23 December 2024
The initial process involved carefully melting pine rosin on a low heat before slowly stirring in linseed oil. The mixture was then heated to around 170°C and allowed to simmer for about 20 minutes to achieve the right viscosity for impregnation. In parallel, pre-cut flax fibre mats were warmed in an oven to ensure they were completely dry. The mold was prepped with silicone spray and Vaseline for a clean release. The pouring was a delicate layering process: a warm mat, a layer of hot resin, another mat, more resin, and so on. After tapping the mold to release air bubbles and a brief cooling period, the lid was clamped down HARD to compress the layers. The block was then de-molded for a final, low-temperature cure in the oven.
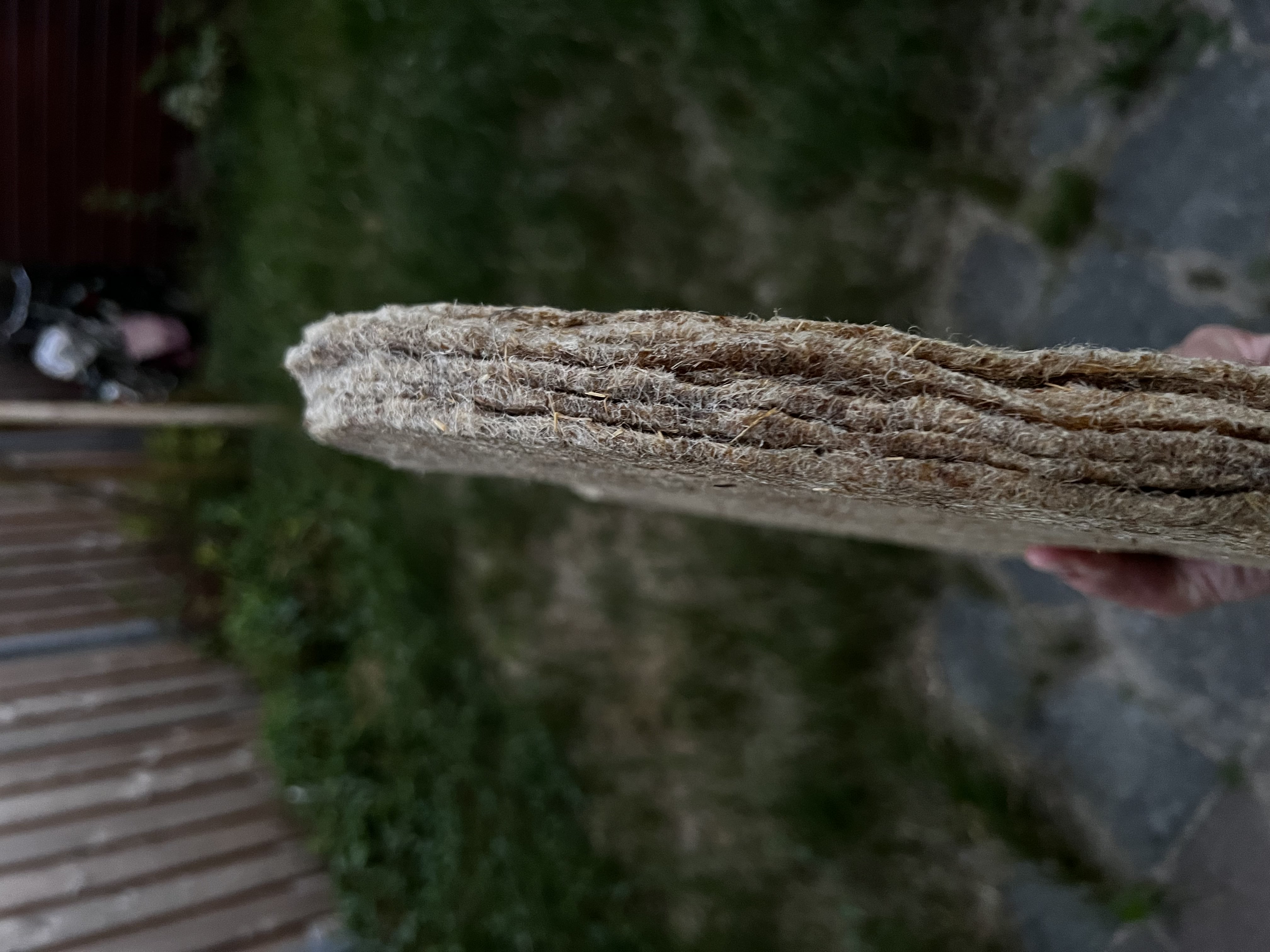
The process involves careful layering of the flax mats and resin in a compression mold. After curing for several weeks, the result is a surprisingly stiff blank, ready for shaping, routing, and finishing just like a traditional wooden body.
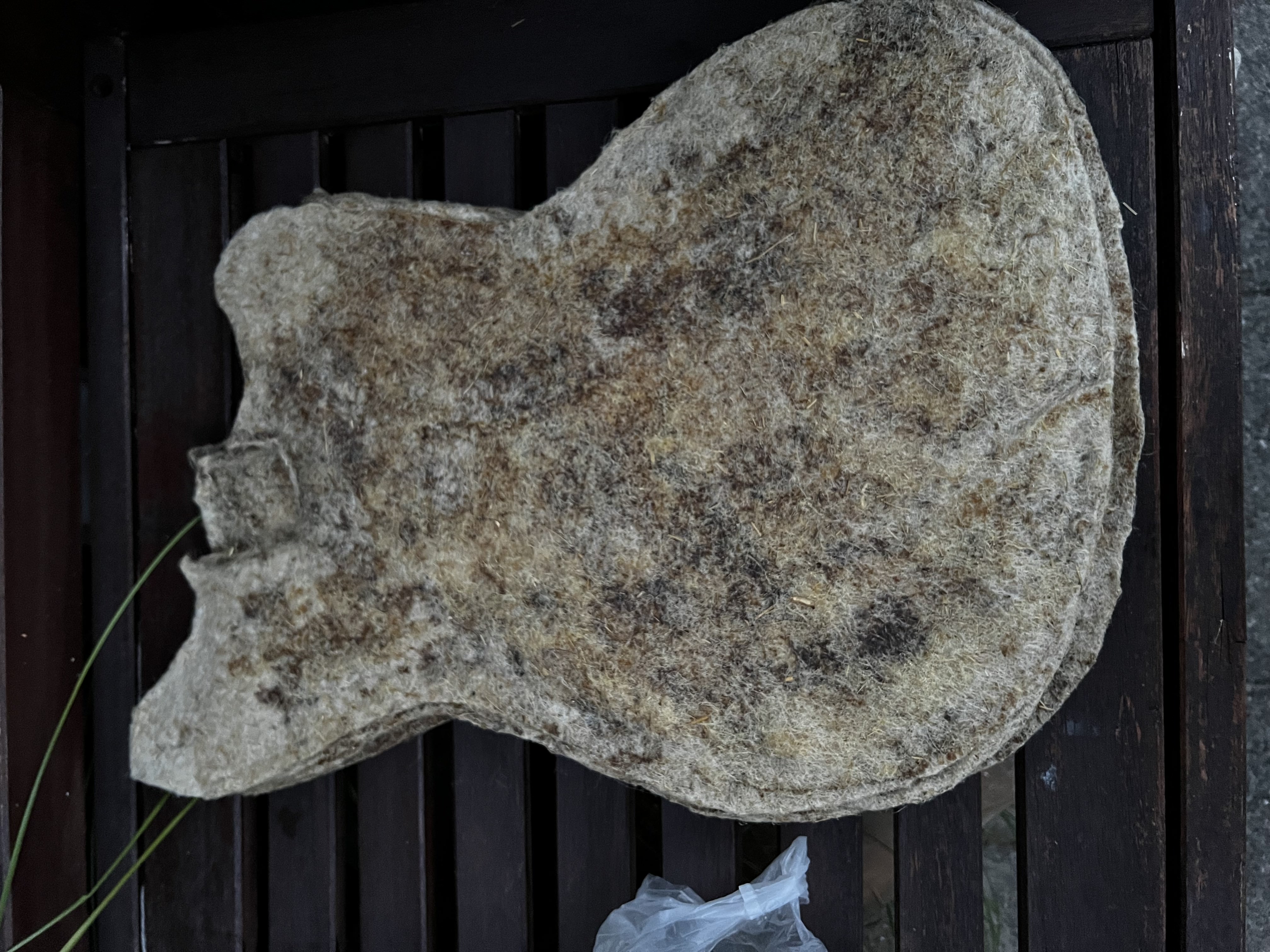
V2 January 5, 2025 & Lessons Learned
The first attempt seemed to have way too much linseed oil which made drying a slow slow nightmarish process. For the second attempt I doubled the rosin so that the linseed to rosin ratio was 1:1.
The next step is to build these out with necks and pickups to see how they truly perform as complete instruments. Stay tuned for updates!